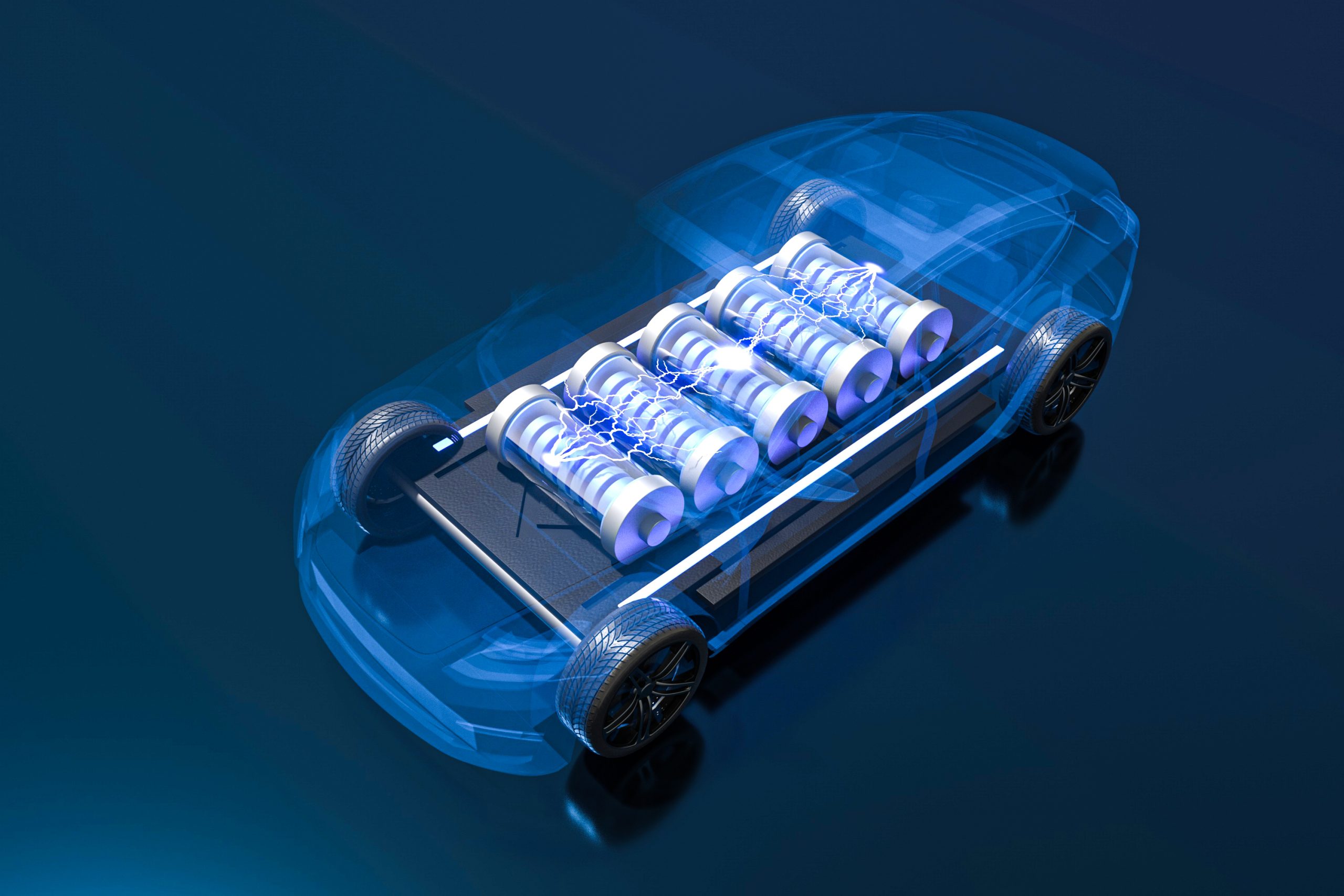
As the global energy transition accelerates, solid-state battery technology remains a key focus in the EV industry. LEAD showcases a fully integrated all-solid-state battery manufacturing solution, encompassing all-solid-state electrode making, electrolyte membrane making and lamination, cell assembly, densification, and high-voltage formation and grading.
By leveraging advanced techniques like dry electrode manufacturing and a highly integrated design, our solution streamlines production, reducing labor costs by 20% and overall investment by 30%. It ensures high efficiency, quality, and compliance with strict environmental and safety standards, setting a new benchmark for all-solid-state battery manufacturing.