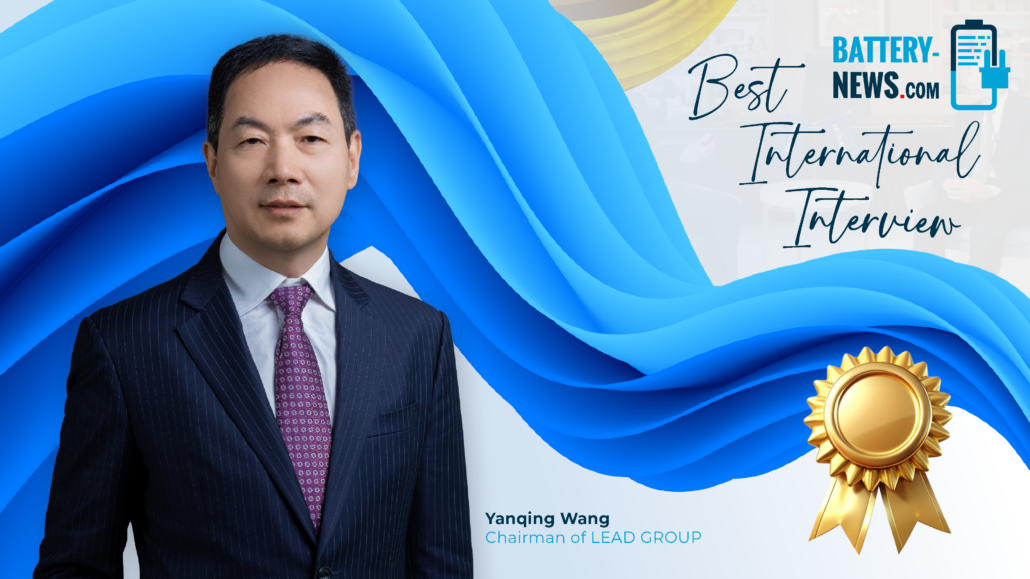
Empowering Energy Transition
with Intelligent Equipment Solutions
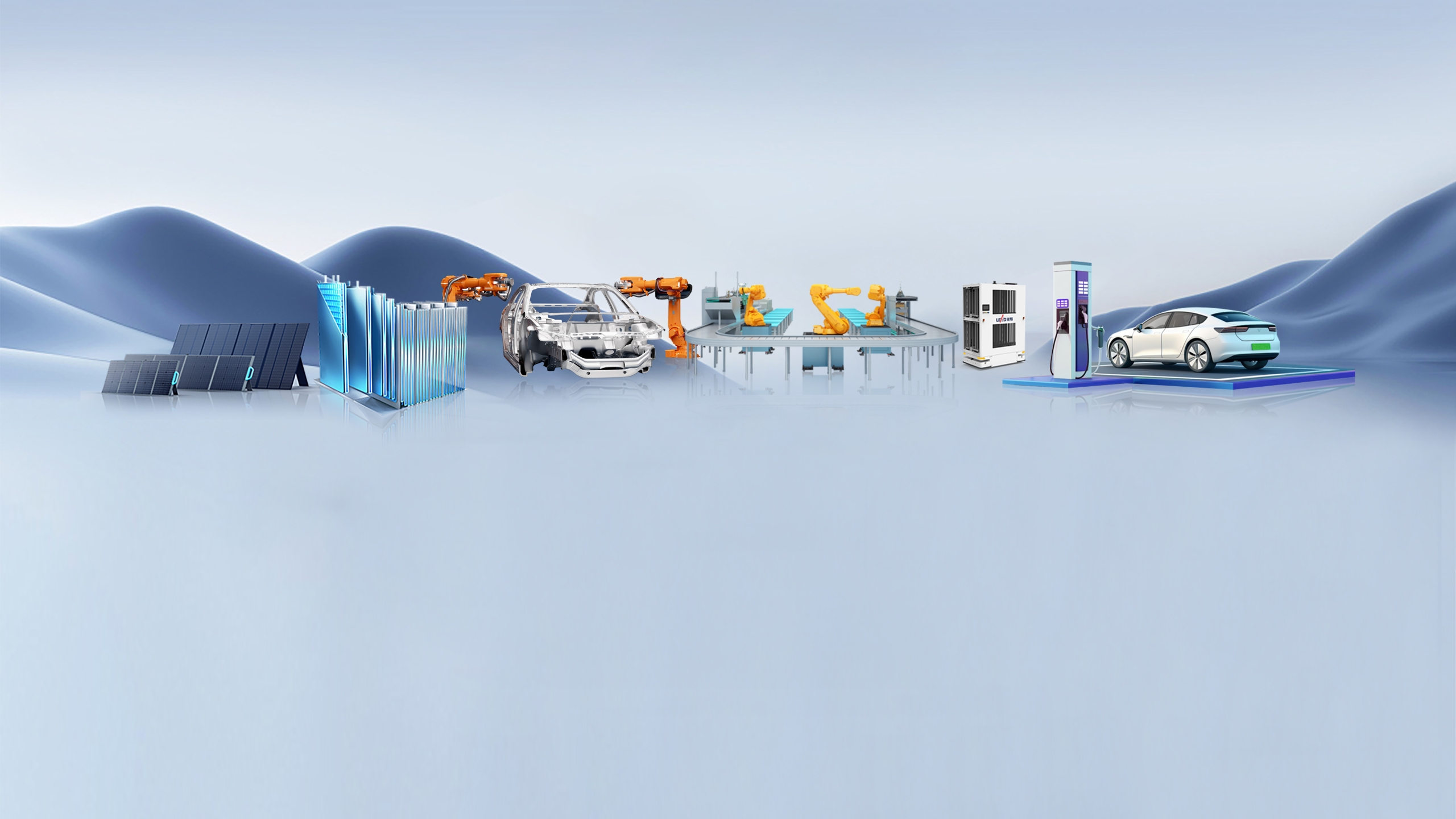
Leading the Way in Digital Infrastructure and Accelerating Industry Intelligence
News
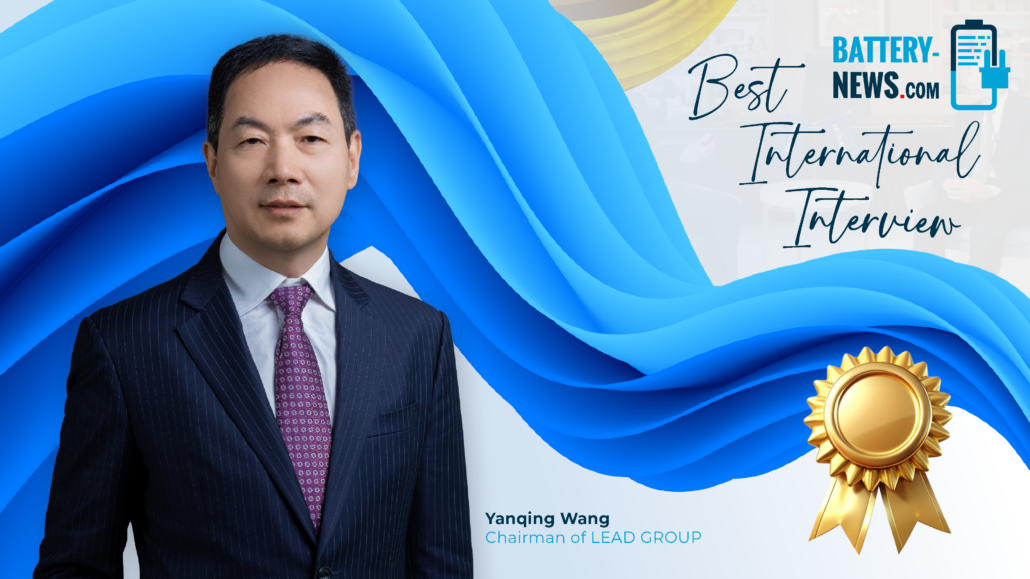
Our Innovation
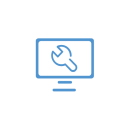
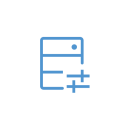
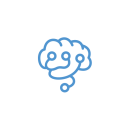
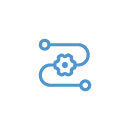

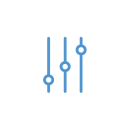
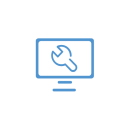
PHM System
PHM System
The PHM system, a pioneering health management and fault detection system for lithium battery production lines, reduces maintenance costs by 30%. It enables rapid fault localization, reducing unplanned equipment downtime by over 40%, and precise fault prediction, enhancing Mean Time Between Failures (MTBF) by more than 20%.
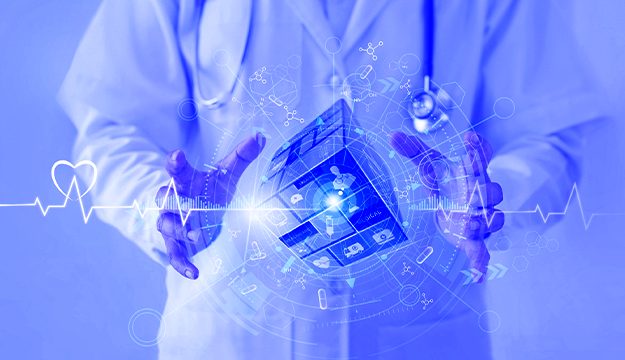
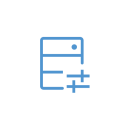
PQM System
PQM System
Leveraging advanced technologies, the PQM system is designed for lithium battery production lines, featuring industry-leading root cause analysis, closed-loop control, and quality prediction capabilities. It ensures product consistency and reliability, accurately identifies non-conforming products, boosts operational efficiency by 30%, and improves overall production yield.
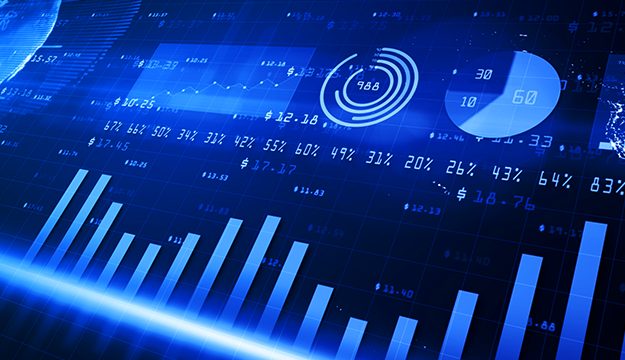
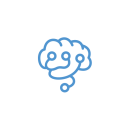
PAI Deep Learning Platform
PAI Deep Learning Platform
This platform supports AI defect detection tasks in industrial settings, facilitating the rapid development of lithium battery visual inspection applications. It offers high sensitivity, scalability, and can be swiftly deployed across multiple clients and locations. The platform includes an industry-first CT image enhancement algorithm and leading AI defect detection technology, ensuring top industry performance benchmarks.
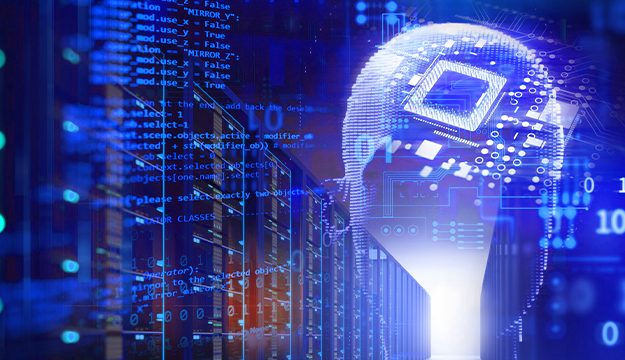
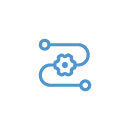
High-Precision Laser Flying Welding Technology
High-Precision Laser Flying Welding Technology
Utilizing vision-based correction algorithms, this high-precision flying welding technology performs real-time laser welding during battery motion, doubling production efficiency and reducing equipment footprint by 30%.
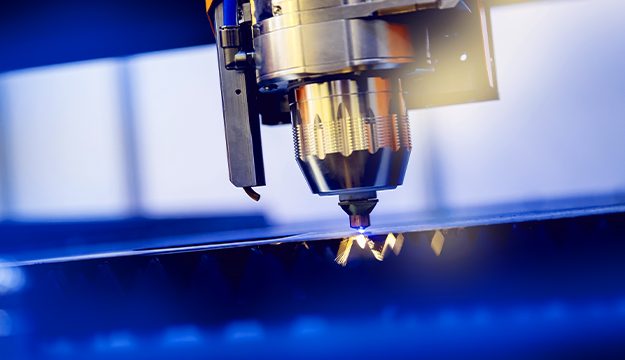

Ultrafast Picosecond Laser Cutting Technology
Ultrafast Picosecond Laser Cutting Technology
This technology employs ultrafast laser pulses for high-frequency coating cutting, effectively replacing traditional die-cutting methods. It offers excellent cutting quality and significantly reduces maintenance costs (saving up to 40 million per year for a 60 GWh production line).
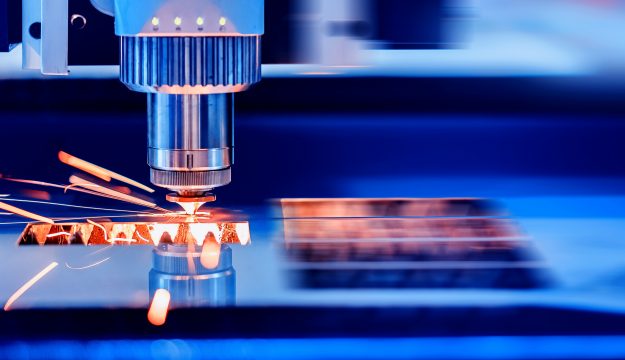
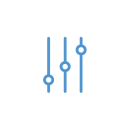
Virtual Debugging Technology
Virtual Debugging Technology
This technology enables integrated electromechanical and software virtual debugging during the design phase, preventing issues such as collisions, safety concerns, process discrepancies, and model alterations. It boosts delivery efficiency by 50% and cuts down design-related issues by 80%.
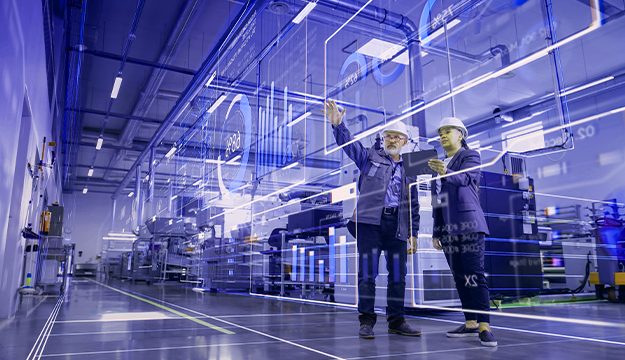
World Leading Intelligent Equipment Manufacturer
Our Businesses
We Provide End-to-End, Turnkey, and Customized Solutions for Your Manufacturing Process
Contact Us
"*" indicates required fields